Moravia Cans is committed to designing and producing the most innovative, lightweight, and sustainable aluminium aerosol cans in the market. Managing Director, Martin Boaler, updates us on recent developments.
A CAN-DO ATTITUDE TO AEROSOLS
Since featuring Moravia Cans (Moravia) at the beginning of 2021, many significant events have impacted the development of all business environments.
The packaging and containers sector is no exception, as it has been affected by the COVID-19 pandemic and ongoing conflicts in Ukraine and the Middle East.
However, the resilience and continuity of metal packaging as a leading and increasingly sustainable solution has been remarkable, whilst Moravia’s focus on the highest specification of aluminium monobloc aerosol cans, principally for personal and home care markets, has also remained unwavering.
“We supply almost every major aerosol brand owner, plus many more local market players,” states Managing Director, Martin Boaler.
“The company is now also diversifying into containers for adjacent markets, such as drinking water, alcoholic, and non-alcoholic beverages.”
“On a product-by-product basis, Moravia’s offerings have always been lighter than the competition”
Martin Boaler, Managing Director, Moravia Cans
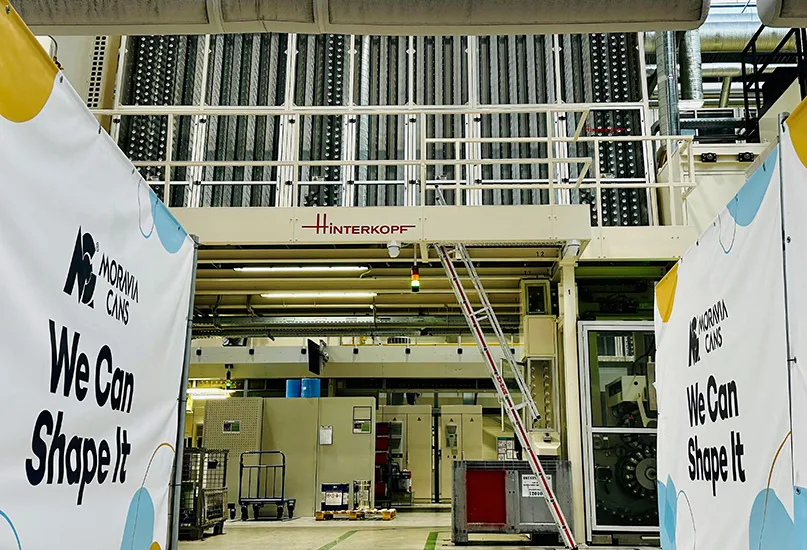
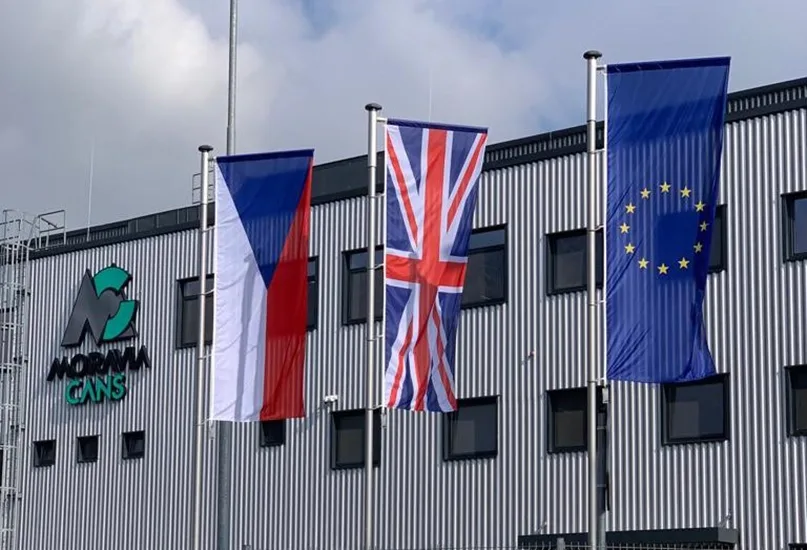
LIGHTWEIGHT PRODUCTS
Based at a single world-class manufacturing facility in Bojkovice in the southeast of the Czech Republic, Moravia has operated in its current guise for over 30 years.
The company has always been focused on the design and production of the most sustainable products in its market segment.
Lightweighting in particular has been the number one priority in Moravia’s drive to increase the sustainability of its monobloc aerosols and bottles.
“On a product-by-product basis, Moravia’s offerings have always been lighter than the competition,” acclaims Boaler.
“This has been achieved by investing in the highest capability production machinery and then further optimising this machinery through leading R&D to enable the production of complex-shaped products at the same weight and speed as standard products from our competitors.”
Wall ironing has long been adopted as part of the company’s standard impact extrusion process, enabling lower wall thickness with improved surface quality and reduced weight.
This lightweighting was further enabled by moving to proprietary patented alloys that maintain the highest strength after required curing processes.
A significant proportion of Moravia’s production has recently been moved to the coil-fed drawn and wall-ironed (DWI) process that is usually more associated with beverage cans.
“The greater consistency of the coil input material, together with the faster and more controllable DWI production process, enables long-run specifications to be produced with increased speed and quality,” Boaler informs.
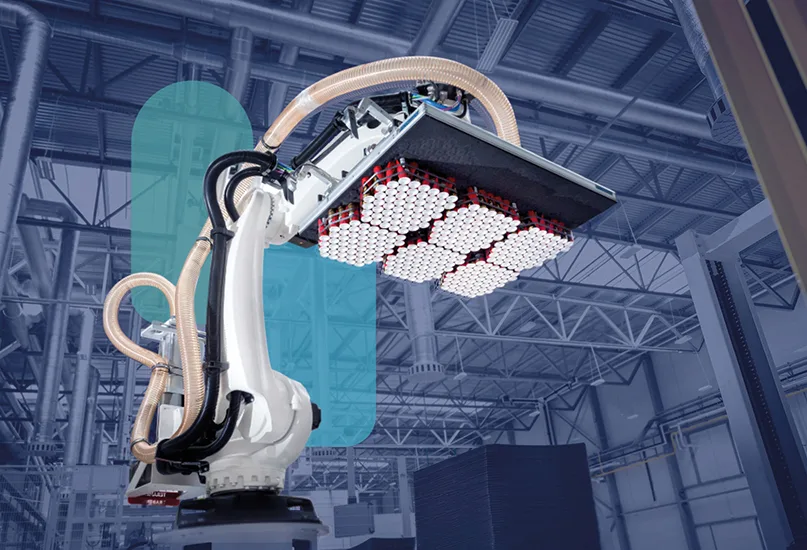
INCREASED CAPACITY
Moravia has undergone significant industrial development and increased its output volumes since we last featured the company just under four years ago.
Indeed, it has grown its production capacity by almost 20 percent in that time, which has improved efficiency by a similar amount across the whole operation.
“We will now make further changes to increase capacity and efficiency by similar additional percentages over the next two years,” outlines Boaler.
The broadening of Moravia’s product range to include more top consumer brands has likewise contributed to its recent growth.
“We have grown in all respects, with 30 percent being organic with existing customers across their product portfolios,” he reveals.
“The remaining 70 percent of our recent growth has come from new customers and through the development and implementation of our new products and processes.”
The company also plans to heavily invest in its production lines over the next two years, prioritising front and back-end automation.
It has already added an 11th production line, which is now running at full capacity, whilst a 12th is currently being implemented. Both of these lines are state-of-the-art and based on Moravia’s market-leading DWI product technology.
This will be a logical continuation of Moravia’s long-term capital investment strategy and revolutionise its manufacturing footprint.
“We will densify our production and concentrate this over two fewer production halls,” Boaler tells us.
“This will enable increased harmonisation of end-of-line processes between lines with improved integration into warehousing and upstream and downstream logistics.”
Additionally, the company will be retiring some outdated lines and sections of lines to enable 100 percent of its production capacity to run Moravia’s market-leading product standing in both DWI and impact extrusion with ironing (IEI).
“Maintaining this load balancing flexibility between the two formats has been a priority to ensure the best continued alignment with the customers and market that we
serve,” notes Boaler.
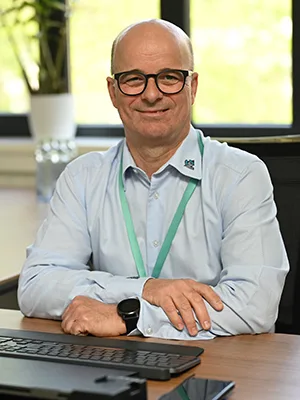
“We believe our increased focus on manufacturing excellence, allied to our continuing leadership in R&D, can move monobloc products to new levels of performance”
Martin Boaler, Managing Director, Moravia Cans
SUSTAINABLE ALTERNATIVE
Moravia’s status as an industry leader is demonstrated by its EcoVadis Silver rating and long-standing ISO 9001/14001/45001 and BRC accreditations.
Complemented by other local environmental, health, and safety (EHS) accreditations, including the company’s own ‘Vision Zero’ approach, these ‘license to operate’ necessities have focused Moravia on continuous improvement and maintaining the most exacting standards.
“We are now also fully focused on the most relevant accreditations in sustainability and have a clear action plan to move to EcoVadis Gold and beyond,” discloses Boaler.
The company has also identified the Aluminium Stewardship Initiative (ASI), CyberVadis, and Sedex as focus areas for accreditation and continuous improvement.
This is in addition to much more active participation in relevant industry-wide initiatives through Metal Packaging Europe (MPE) and the Metal Packaging Manufacturers Association (MPMA).
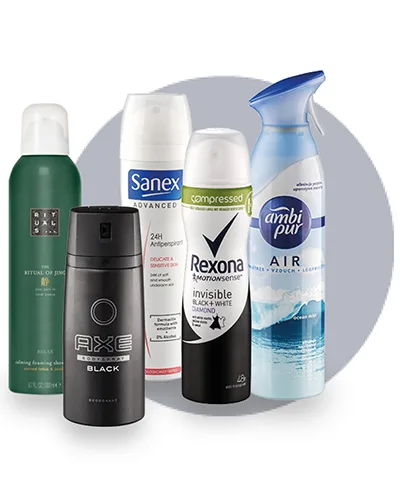
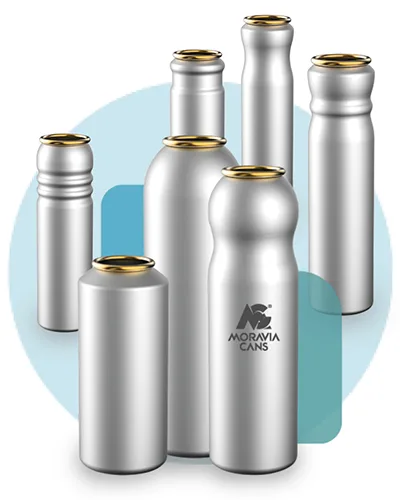
Operating in a highly competitive market, Moravia recognises the need to prioritise promoting and enhancing the position and perception of metal packaging against less sustainable and capable alternatives.
The focus has always been on bringing product excellence, which has included full body shaping, to the market, with others then following suit.
“We believe our increased focus on manufacturing excellence, allied to our continuing leadership in R&D, can move monobloc products to new levels of performance,” Boaler concludes.
“Moravia has always had an exclusive focus on the aerosol market, and we are now adding other relevant adjacent portfolios to this approach.”
The next few years will see some interesting developments in aluminium monoblocs at customer, product, and consumer level, and Moravia aims to remain at the forefront of these exciting times.