As Romania’s premier poultry product provider, Transavia is dedicated to quality and flavour with its family-run business. We tuck into the company’s processes, portfolio, and prospects.
BUILDING FARMS CHICK BY CHICK
Since Transavia’s inception in 1991, it has continually made astute investments. Today, the company owns the most advanced vertically integrated poultry business system in Romania. However, quality products and innovation have also contributed to its success.
As the local leader in the poultry industry, the company was founded when Eng. Ioan Popa purchased a former agricultural farming cooperative for cows and transformed it into a broiler farm. Transavia then positioned itself at the forefront of the Romanian chicken meat industry in eight counties and has since become a reliable partner in the export market.
Transavia has strived to improve upon the from farm to fork mantra for healthy eating by championing its own from grain to fork process. Its integrated operation includes grain production, harvesting and accommodation for feeding chickens, breeding and broiler farms, a meat processing plant and product distribution.
The benefit of an integrated structure allows for governance over each aspect of food safety. Transavia can maintain biosecurity measures, vaccination programmes, and testing for bacteria such as salmonella at breeder farms and hatcheries. Moreover, in the feed mill, strict pest management controls the spread of disease.
With continual enforcement of all standards, it was inevitable that Transavia became the only company to have a code of conduct at the European level for the food industry. Additionally, in 2006, Transavia achieved the title of Supplier of the Royal House of Romania as well as winning other national and international awards. High-quality standards exist throughout its poultry breeding and food production processes and are therefore central to the company’s success.
THE POULTRY PROCESS
In 2011, Transavia established four vegetal farms situated within the limits of 58 localities in Transylvania to form its agricultural division, becoming the first poultry producer to provide chicken feed from its own sources.
Cultivating grains, wheat, and corn with high-performance agricultural equipment, Transavia had to extend the following phase. In 2015, the production and storage capacity of its feed mill factory was forced to increase by 70 percent.
The feed mills are provided with a fodder sterilisation system unique to Romania. Furthermore, the mixed feed fodder factory in Alba produces around 500 tonnes of feedstuff per day for Transavia farms without any contact with the external environment.
In order to avoid contamination, the 24 broiler farms are located within areas isolated from other animal farms, and there are separate rooms for each operation in Transavia’s two hatching stations. With the volume of eggs produced at the reproduction farm, the poultry is carefully selected, and their health is monitored by a sanitary veterinary laboratory.
Meat products are subsequently packaged under a controlled atmosphere and stored in the freezer or refrigerating areas from where they are distributed under the safest conditions by using vehicles from Transavia’s own fleet.
The production lines are equipped with cutting-edge technology, which transforms the meat into finished products by fully automated operations.
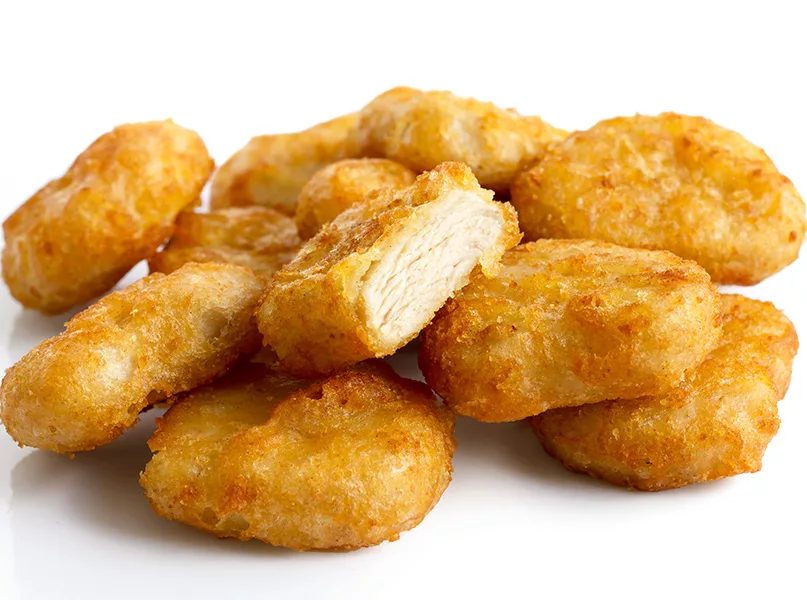
THE PRODUCT PORTFOLIO
The most recognisable brand in the Transavia portfolio is McDonald’s, but the iconic golden arches are not only associated with hamburgers and fries. Indeed, since its partnership with Transavia began in 2017, the fast-food restaurant has used around 5,000 tonnes of the company’s chicken meat.
McDonald’s has high global standards which require specific technologies, and becoming a supplier is an uncompromising process with strict rules, but Transavia has risen to the challenge.
In 2021, McDonald’s introduced a menu of superior products using 100 percent locally produced chicken. Together with Transavia, the famous eatery developed products that were an instant hit. The launch of Supreme Chicken Tenders was a collaboration that was extremely well received by the Romanian public. This was thanks to the Transavia range, Fragado, which is recognised for its high quality, tenderness, and flavour.
This premium brand includes a range of fresh meat products which are portioned to serve individual customers and hotel, restaurant, and catering professionals. Under the Fragedo umbrella, the company has developed Fragedo Deli sub-brands, Barbecue, Marinés, and Selected Assortments, and Vin Prietenii la Tine – ready to cook specialities based on Transavia’s own recipes.
Papane, and the Papane Bistro range, offers a quick chicken fix with menus designed for active lifestyles, but also for those who want to eat healthily. State of the art technology is used to cook and freeze schnitzels, nuggets, burgers, and goujons, which also allows them to keep their taste and texture. Meanwhile, the Libertan range is natural, ethical, technologically advanced, and sustainable in terms of rearing chickens and processing the meat.
As consumers are always at the centre of Transavia’s business, its goal is to provide the best quality chicken meat, while focusing on market developments and local and international trends.
SUSTAINABLE INVESTMENTS
Transavia is committed to investing in renewable energy by adopting efficient technologies and equipment. With several projects that are already underway, this year the company will install 22,000 photovoltaic (PV) panels to produce green energy. This will eliminate the equivalent of the annual carbon emissions from 1,778 cars from the atmosphere.
The PV panels will be installed on the roofs of poultry farms and on the ground, depending on the structure of the buildings and their position in front of the sun. Currently, more than 100,000 square metres of PV panels are due to be fitted.
In addition to the PV panels, Transavia will implement two cogeneration projects with high electrical and thermal efficiency. The initiative is part of a sustainability strategy to minimise the company’s carbon footprint. By the end of next year, it should be able to produce 80 to 100 percent of the energy it needs.
To enhance the efficient use of energy, Transavia has specific measures in each operating unit. Thermal insulation of some houses and the microclimate automated monitoring equipment in the broiler house will aid the reduction of energy consumption that the company has already made by replacing existing light fixtures with LED. Moreover, Transavia uses natural gas to produce steam that ensures technological flow to heat the chicken houses and administrative areas.
The significant reduction in carbon emissions will also have a positive economic effect as the benefits of Transavia meeting its own sustainability needs mean that the company will be protected from fluctuations in energy prices.
With 32 years of experience, Transavia continues to evolve and innovate by embracing modern technologies. However, the next step for the company is to expand international cooperation, strengthen existing partnerships, and increase exports.