We speak to Milan Kvetko, Commercial Director of SLOVMAG, a.s. Lubeník, about enhancing the handling and processing of refractories in Slovakia.
MATERIALS TO HANDLE THE HEAT
“A 60-year-long tradition of shaped refractories production, as well as vast experience with the diverse chemical, mechanical and thermal conditions in furnaces of various types, helps us to provide our customers with the most suitable refractory solutions,” opens Milan Kvetko, Commercial Director of SLOVMAG, a.s. Lubeník (SLOVMAG).
Used in furnaces and kilns, refractory materials must be chemically and physically stable at the highest temperatures.
Of the most important materials used to manufacture refractories, namely the oxides of aluminium, silicium and magnesium, SLOVMAG produces materials on a magnesia basis to be utilised for heat aggregates linings.
Since 2008, SLOVMAG, one of the largest producers of refractory materials in Slovakia, has been a member of Russia’s number one refractories producer, Magnezit Group, who own several factories including the country’s largest refractory brick production facility.
Kvetko adds that the cost-effectiveness of the refractories supplied are taken into consideration.
“Our flexibility makes it possible to react even to our customers’ most specific refractory requests. Our R&D in new products helps our customers to prolong the lifespan of refractory linings in their furnaces, thereby increasing their performance whilst creating a safer working environment.”
“We consider customer satisfaction as the most important condition for the long-term success of our company”
Milan Kvetko, Commercial Director, SLOVMAG, a.s. Lubeník
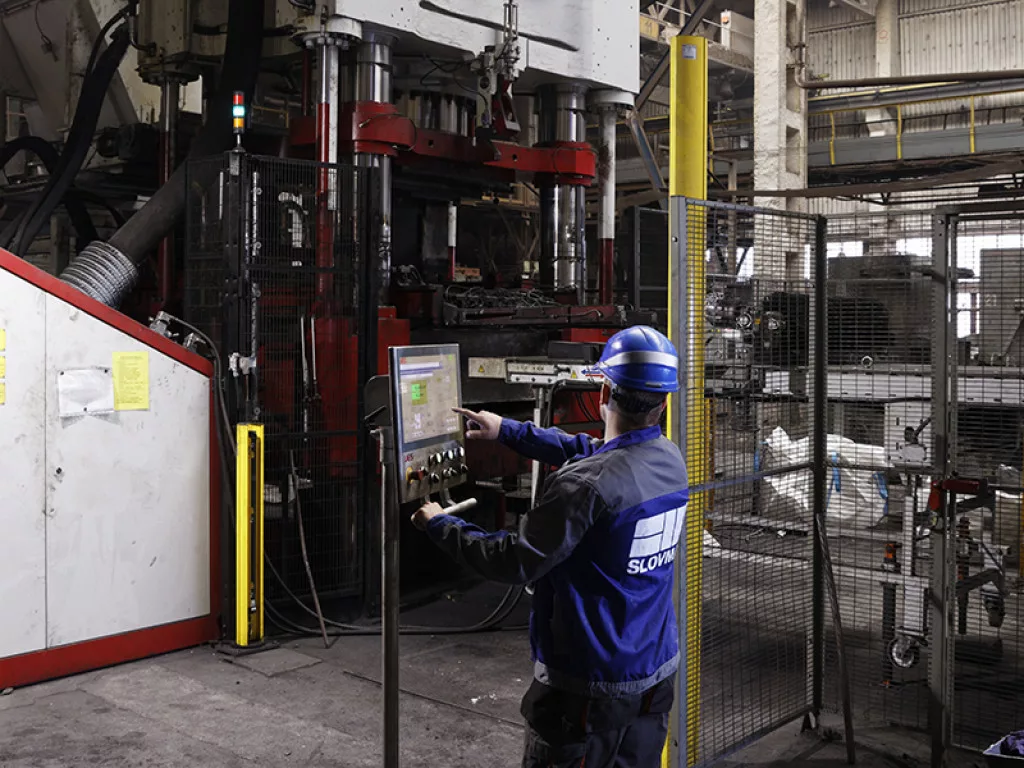
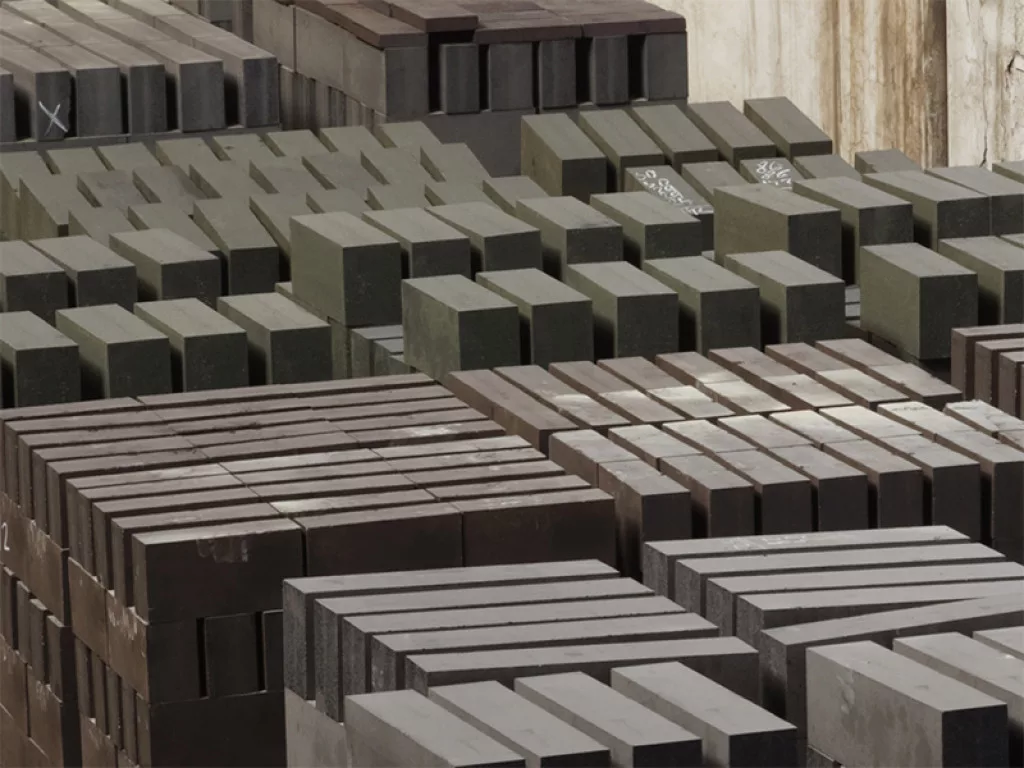
MADE FROM MAGNESIA
The steel industry is the biggest consumer of basic refractory products, which are used to line high-temperature equipment.
Operating its own magnesite mine, processing and manufacturing facility, SLOVMAG’s product portfolio for the steel sector includes a line of magnesia, magnesia-chromite and magnesia-carbon shaped bricks, supplemented by unshaped mixes and mortars.
Although refractories aren’t visible as a final product, they are part of the production process in many industries. As such, there are more than 550 shaped products with different physical properties and chemical compositions across SLOVMAG’s entire portfolio, which also caters for non-ferrous metallurgic, cement, lime and storage heating applications.
“We can produce these products in approximately 2,000 various shapes, and the portfolio is complemented by almost 200 different bulk products,” reveals Kvetko. “Linings for the production of steel, lime, cement and non-ferrous metals cannot perform without our bricks.
“The unshaped products, made of dead-burned magnesia and various additives, include ramming and gunning mixes, mortars and filling mixes. In addition, we can flexibly adapt to specific customer requirements and create the required quality for them, thus expanding our production portfolio.”
A few years ago, SLOVMAG achieved FAMI-QS certification, the worldwide Quality and Feed Safety Management System for the sector of Specialty Feed Ingredients, before penetrating the caustic calcined magnesia market, which is used as an additive in agricultural compound feed or industrial fertilisers.
“We consider customer satisfaction as the most important condition for the long-term success of our company,” Kvetko emphasises. “This is why we do our best to manufacture high-quality products and to support them with high-level technical solutions and services.”
“Our R&D in new products helps our customers to prolong the lifespan of refractory linings in their furnaces, thereby increasing their performance whilst creating a safer working environment”
Milan Kvetko, Commercial Director, SLOVMAG, a.s. Lubeník
GLOBAL FOOTPRINT
SLOVMAG delivers products to countries around the world, predominantly in the European Union, Eastern Europe as well as the likes of the Balkans, Turkey, US and the Middle East.
As the company’s product range covers several industrial territories, SLOVMAG’s business partnerships consist of both long-term and short-term contracts for many sub-contractors, whether they are smaller or bigger companies in the region. The supply chain is managed centrally, with most suppliers located in Slovakia and some relationships spanning over 20 years.
“We have verified suppliers, but we also establish cooperation with new contractors,” Kvetko outlines. “Stable cooperation, high-quality products and services in our business network ultimately create a symbiosis of successful outcomes for all participants.”
For several years now, SLOVMAG has been significantly addressing the renewal and modernisation of its production facilities and premises. Despite the challenges surrounding COVID-19, this hasn’t stopped SLOVMAG from investing in new equipment to enhance the handling and processing of materials.
Existing presses have been overhauled, whilst new presses, press moulds, a CNC milling machine and chamber hardening furnace have been purchased to support the company’s expanding product portfolio, satisfy specific customer requirements, as well as increase flexibility and independence from external service providers.
“We are continuing to modernise the laboratory with new vibrating mills, muffle furnaces and a benchtop spectrometer to make the work in the laboratory more efficient,” adds Kvetko. “A new drilling rig in our mining operation will also reduce the financial burden of repairs whilst ensuring safety and efficiency in the extraction of raw materials.”
Last year, SLOVMAG trialled the operation of an automatic measuring system (AMS) for measuring emissions that occur in shaft furnaces during the firing of magnesite raw material. At the treatment plant centre, the company replaced two dedusting devices to ensure the reduction of solid pollutants in the working environment by returning the dust collected back to the production process.
Meanwhile, the launch of a project to modernise the preparation of pressing materials, which involves the introduction of automatic dosing and mixing of materials, is close to completion. This will reduce the consumption of raw materials, electricity, and the emission of solid pollutants.
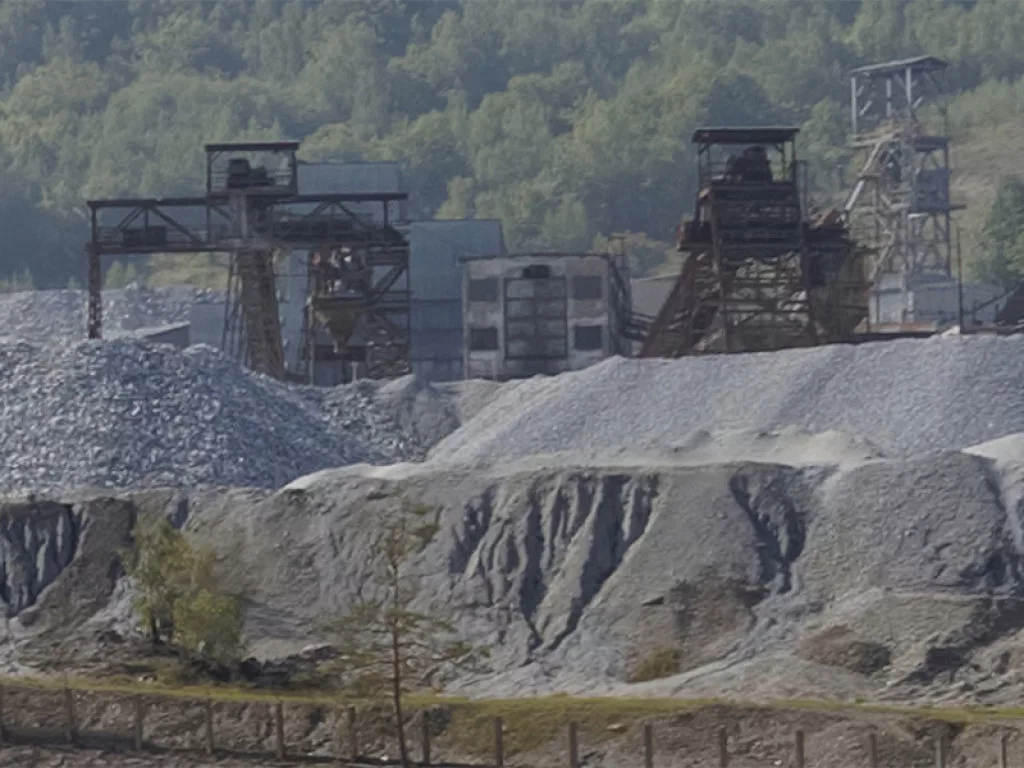
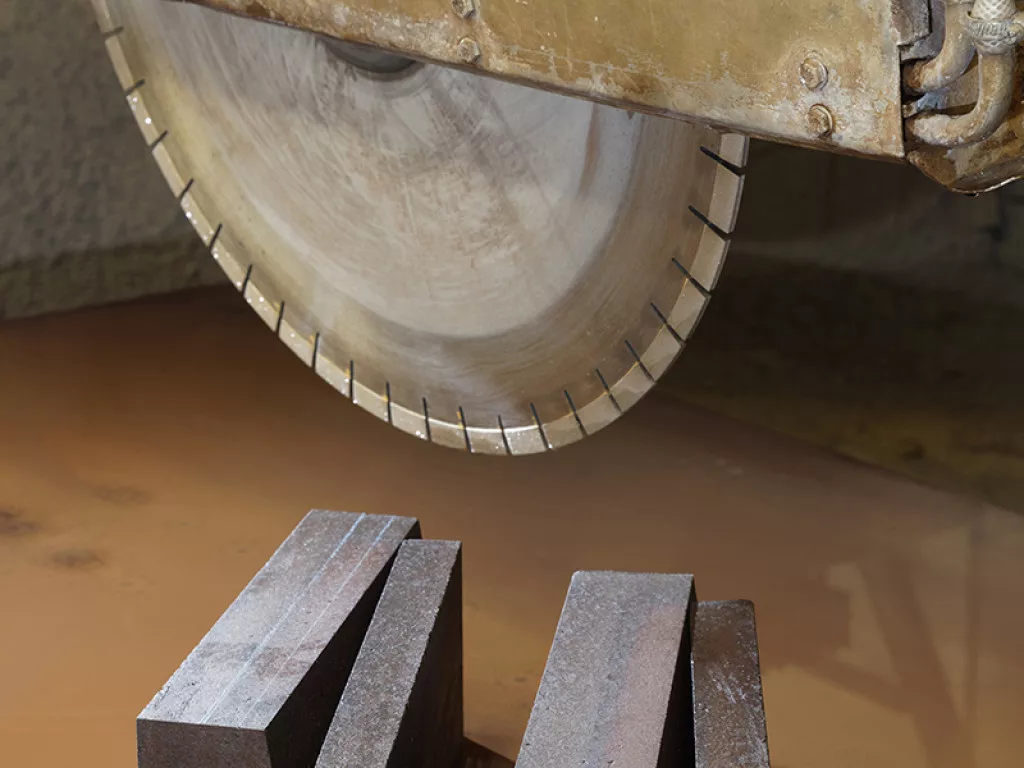
BOOSTED DEMAND
The introduction of robotics, with future investments to be tailored towards an enhanced extraction capacity, is part of SLOVMAG’s ongoing strategy.
“In connection with this, we want to set up and put into operation a packaging line that will reduce the physical demands of the storing and packaging process, whilst increasing the protection of products,” Kvetko says.
“The priority for this year and the following year is also the reconstruction of the tunnel kiln in order to improve the firing quality of our core products.”
Kvetko notes that, due to high transport costs, imports from the likes of China fell sharply and demand for complete products from the European market increased, boosting demand for SLOVMAG’s products as a result.
“As we have invested a lot in recent years, we have also raised our production capacity and can receive more orders. Although demand has increased, we want to continue to meet the requirements of our customers and ensure the quality of our products,” continues Kvetko.
“Specifically, we want to sharpen sales of fired products such as magnesia-spinel bricks to the lime industry, as we have invested heavily in new moulds for special shaft kilns for firing lime.”
Though there is ongoing unpredictability in the market and the world, Kvetko hopes that SLOVMAG will succeed in fulfilling its main goals.
“We also want to raise sales of magnesia-chromite bricks for the non-ferrous metallurgic production of copper and lead. In addition, one of our priorities is the diversification of MgO-C bricks into the steel industry,” he concludes.